Re.Wrap - 90% recycled fabric wrapped panels
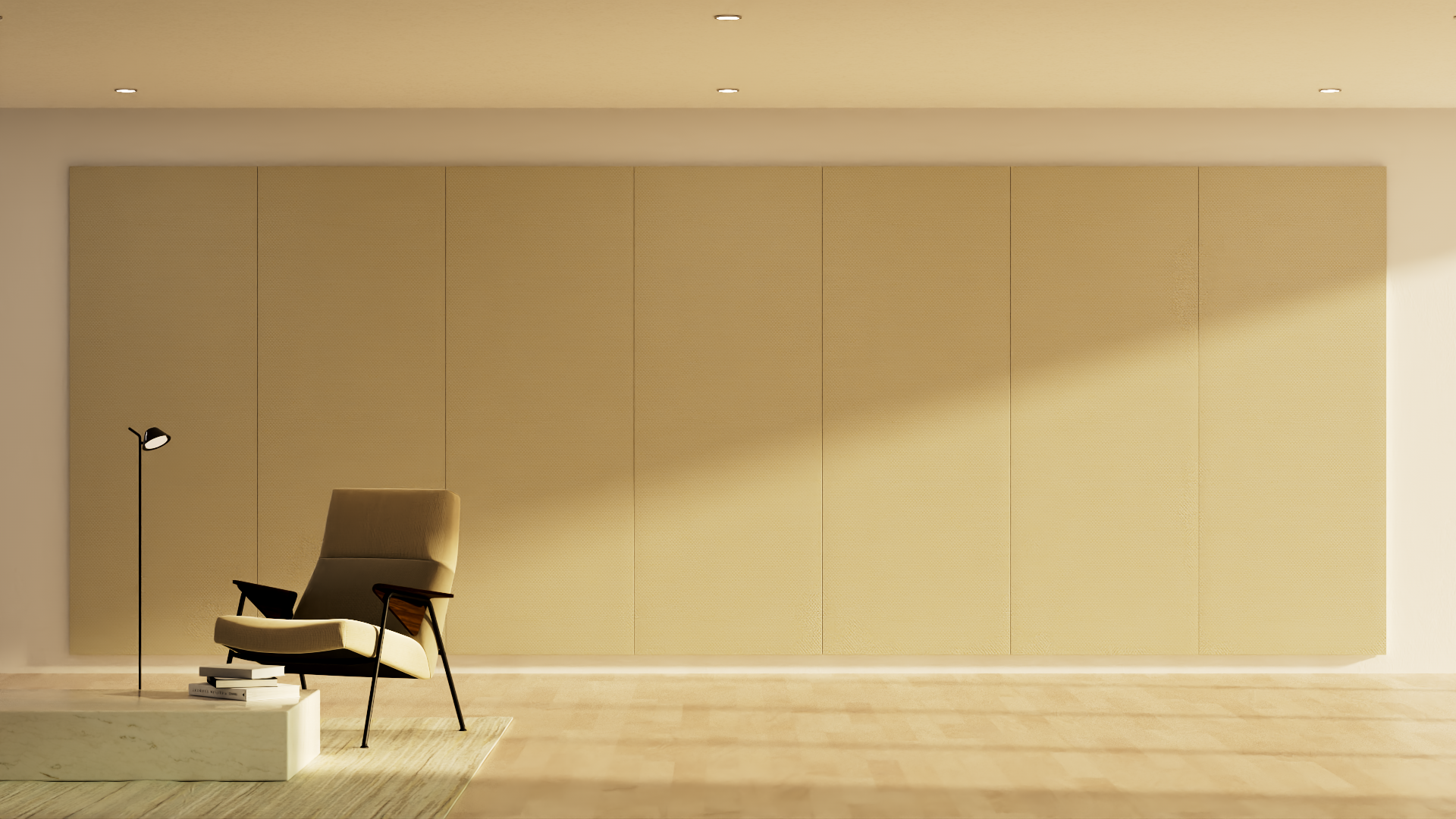
Proudly standing as the world's first 100% recyclable fabric-wrapped acoustic wall and ceiling system made from 96% second-cycle material; Re.Wrap, built in partnership with renowned designer Ric Frampton, translates the coming together of responsibly-driven minds.
The exploration into Re.Wrap began with a straightforward question, 'How do we create responsibly-minded products in a time of material uncertainty?'. New Re.Wrap is able to offer the commercial interiors industry a low-carbon acoustic solution led by material circularity, that takes responsibility for PET waste.
The Collective are dedicated advocates for acoustics in the workspace, understanding their importance and ability to hinder or help us process sensory information. An excessively quiet workplace can be just as distracting as a workspace that is excessively loud. The sound around us greatly affects our productivity and overall well-being. It is also imperative that everything we do here is looked at from an environmental lens - how can we manage the well-being of our people and our planet? So it seemed only natural to partner with Re.Wrap on their new journey and act as the exclusive distributor within the UK and Ireland.
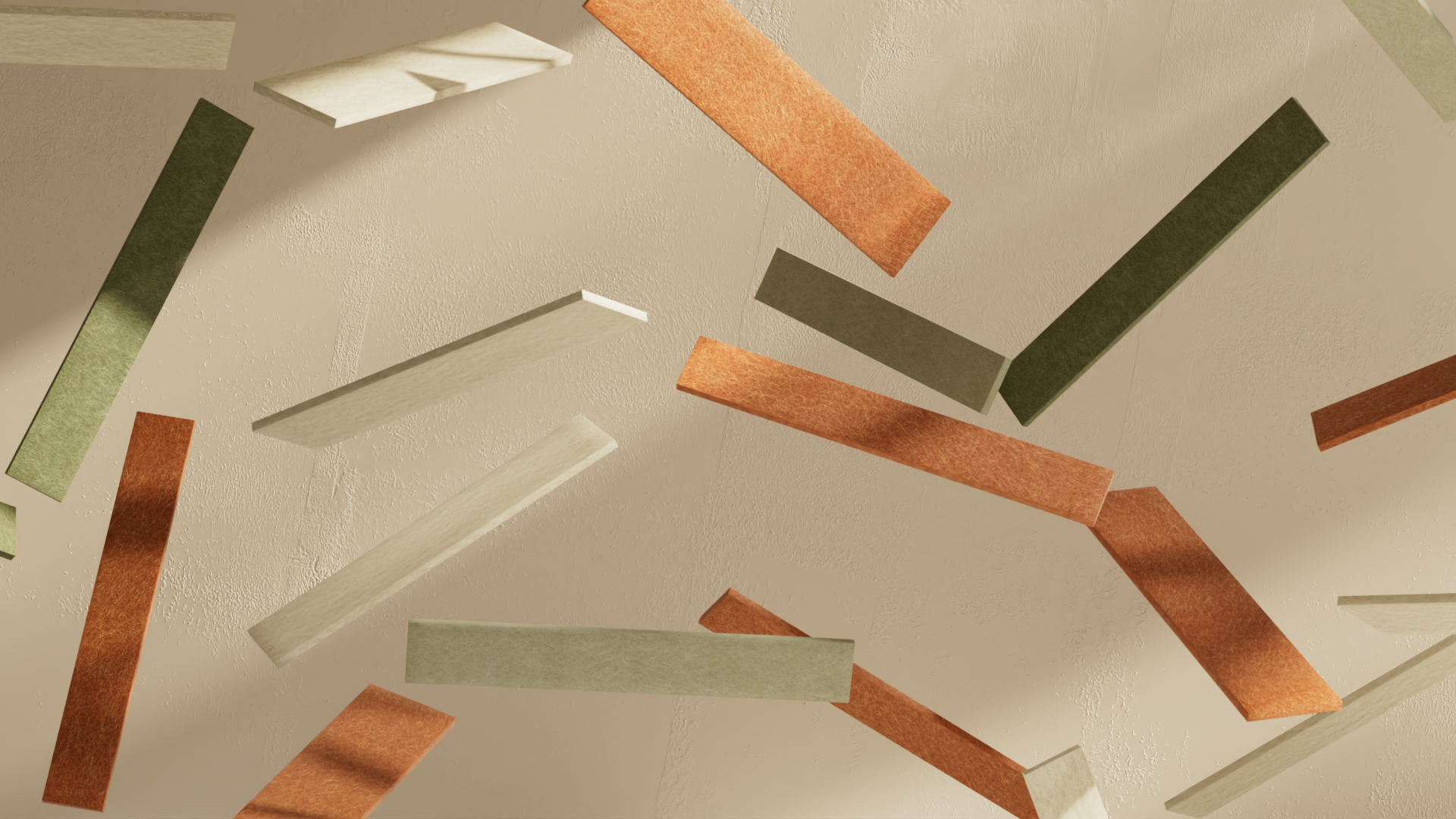
By bringing together the precision 'folding' aesthetics of Origami and the ‘wrapping’ ceremony of upholstery, Re.Wrap represents a new design style for Class A acoustic, fabric-wrapped panels.
Re.Wrap reclaims and revalues second-cycle and waste PET delivering a unique, versatile and responsible Class A acoustic fabric-wrapped system for walls and ceilings in commercial interiors, hospitality and auditorium environments. Championing material circularity, waste recovery, local craftsmanship and creativity, Re.Wrap changes how we think about waste.
The unique and intelligent patent-pending design (2301569.6) that Re.Wrap employs requires zero adhesives and ensures that the product is 100% recyclable, allowing each panel to be entirely disassembled for reuse or refurbishment, and that includes all core parts and fixings.
Building Re.Wrap required developing a new manufacturing process; the key challenge was managing the numerous minor refinements needed during the design process, capturing each core advancement to reach the final product. The result of this was the requirement of only three materials to fully build Re.Wrap; reclaimed PET, aluminium and fabric. Combined they successfully achieve a Class A acoustic performance, an ideal characteristic where wall space is premium and reverberation control is critical. Achieving such a high and tuneable broadband absorbance value requires fewer panels to meet the desired project reverberation levels; which is a key factor when it comes to considering project cost married with an environmental cost.
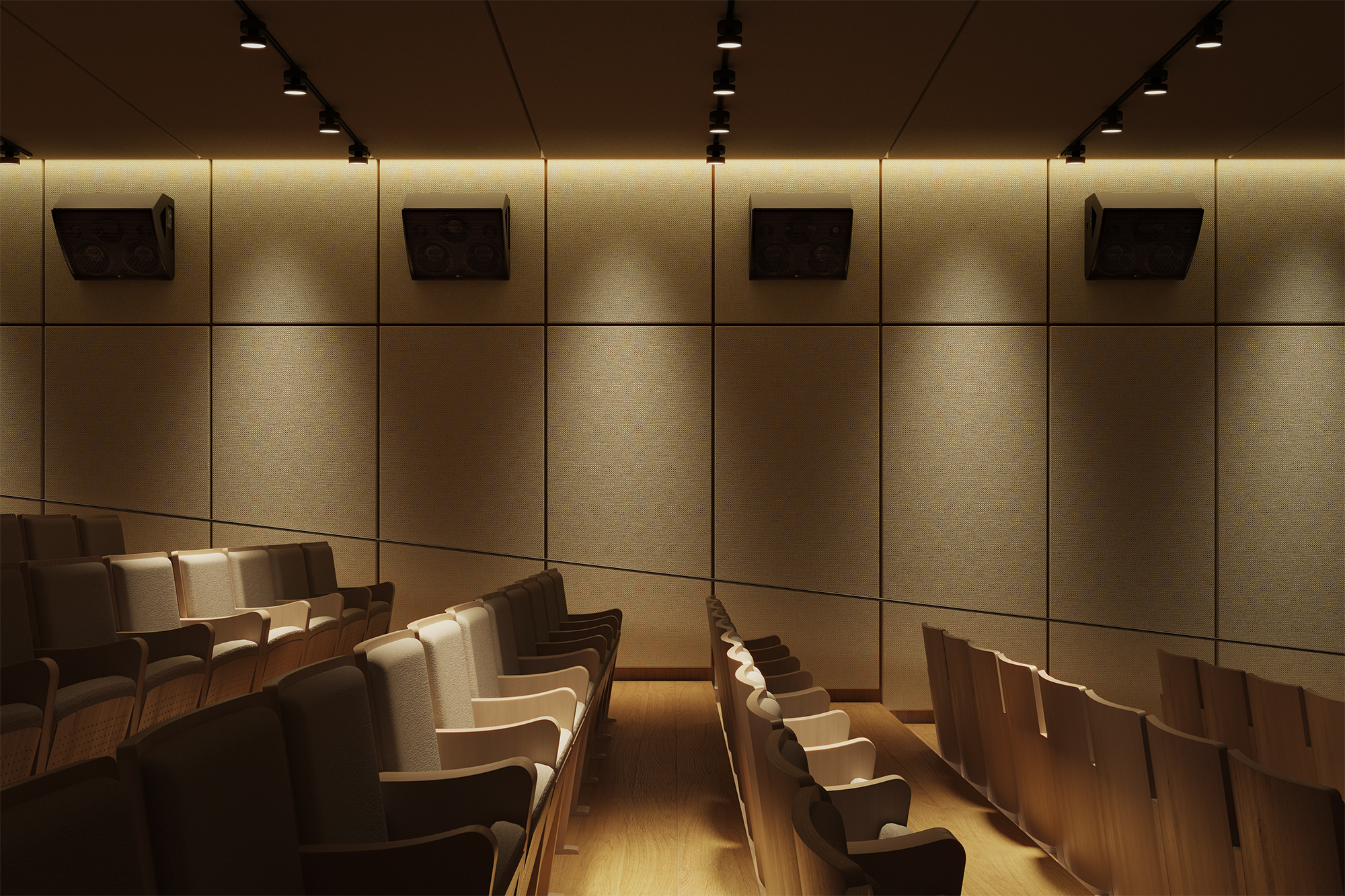
‘As a designer, I understand the importance of my design decisions, the personal effect and implications which can live on for decades outside of my control’, says designer Ric Frampton, ‘The responsibility comes from the ideology of a good custodian of the environment, which Re.Wrap delivers second to none’.
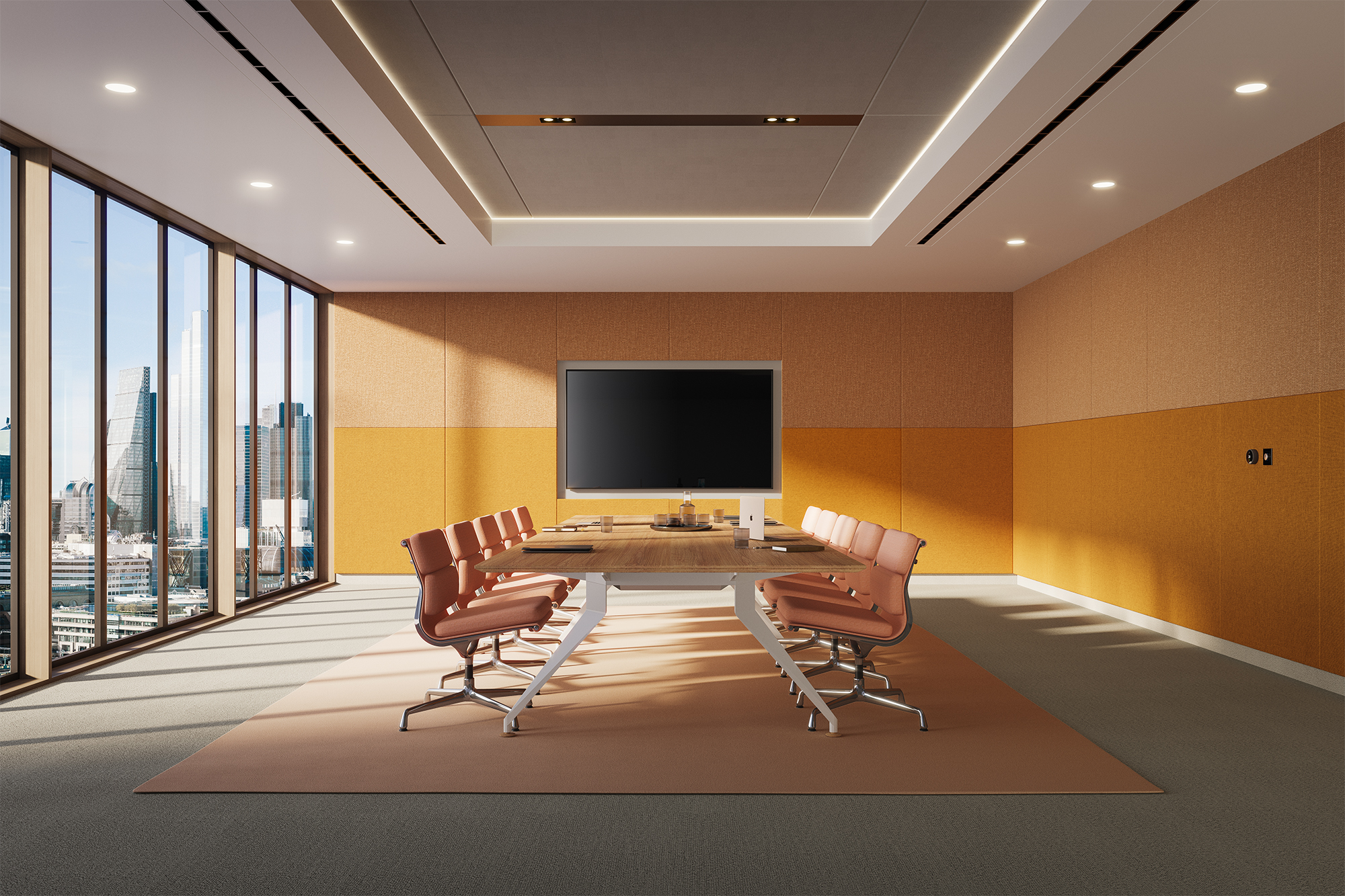
The standard fabric collection offered for Re.Wrap IS carefully selected based on material composition, environmental credentials, acoustic performance and a UK manufacturing base. Project-specific fabric is also available, subject to QC testing and quantity, so the environmental world of fabrics really is your oyster.
Panels are offered in various size configurations, up to a height of 2600mm and width of 1000mm, at increments of 10mm, using a simple, portable wall hanging system and a magnet and cabling solution for ceilings - which secures a straightforward installation process.
To top it all off, Re.Wrap is made in Britain to support local trade and commerce and control carbon usage. Re.Wrap panels are crafted using The Collective's unique complimentary PET ‘Take-Back’ service, which reclaims all disused PET from the industry (including manufacturing off-cuts, damaged panels, or decommissioned interior installations) encouraging second-cycle practices. A material circularity solution for otherwise discarded PET panels.
“A key success of Re.Wrap is how the manufacturing process enables the disassembly and reassembly of all components,’ says designer Ric Frampton, ‘This takes control of closing the recycling loop and sets the materials off on their second or third cycle. The unique Take-Bake scheme strengthens this cycle and creates a continuous loop - a unique and forward-thinking approach .”
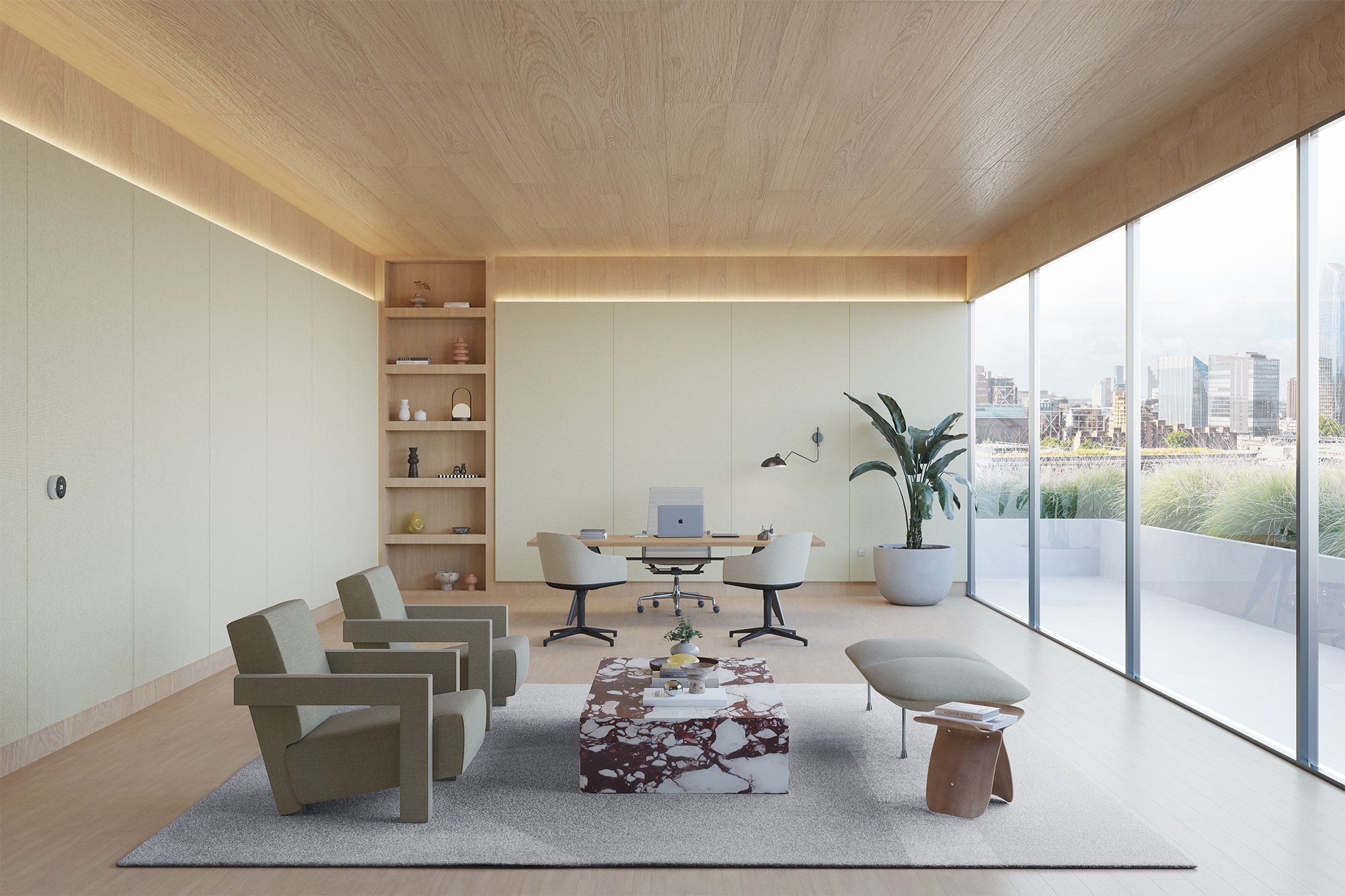