How to design an acoustic wall panel, by Jones & Partners.
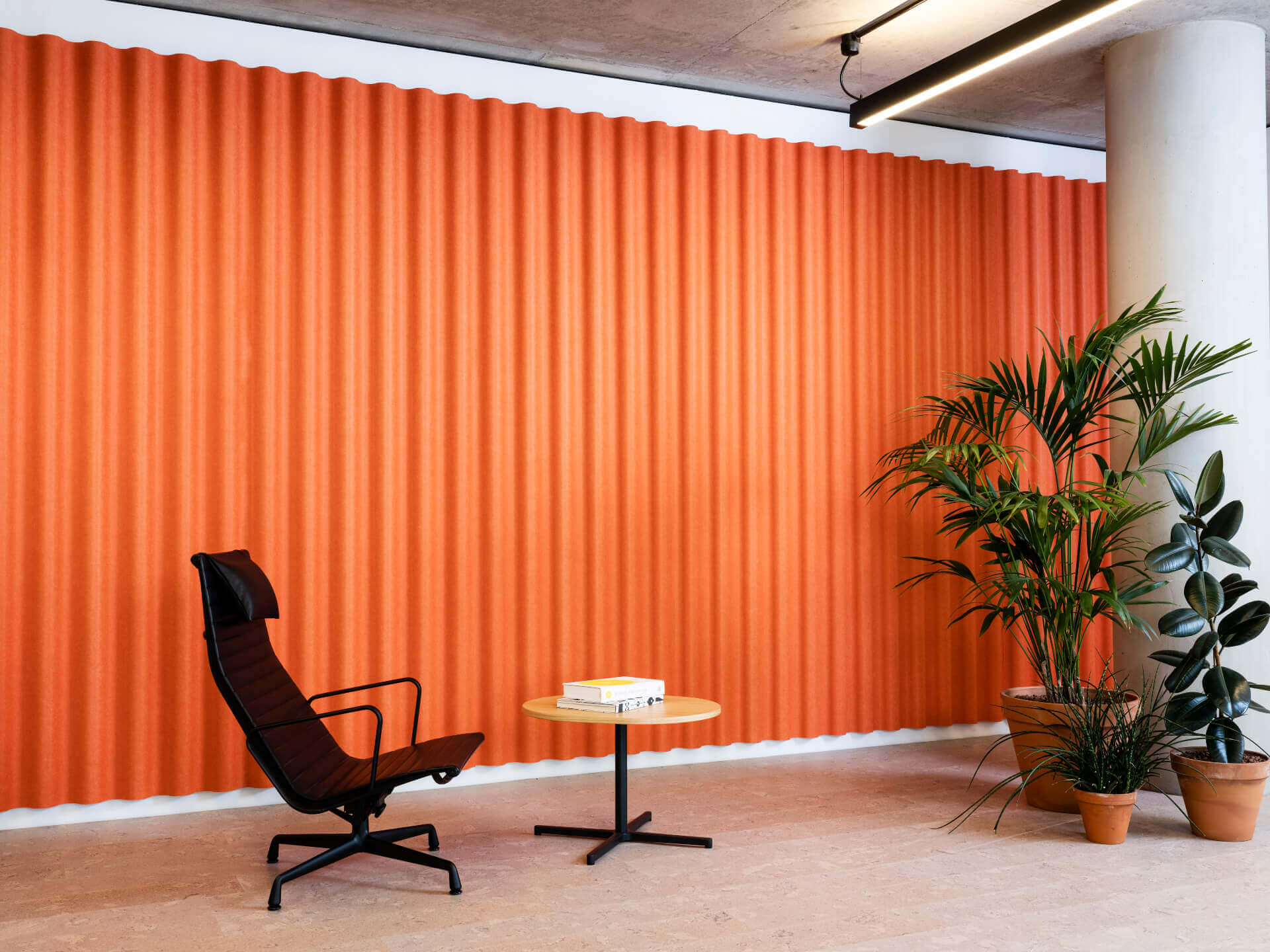
Craig Jones, Director of Jones & Partners discusses the design process, challenges and future development of Swell acoustic wall panel.
(Transcript)
What was the design inspiration behind Swell?
We've been working with The Collective for about two years on different development projects - some furniture, some acoustics. Our first product was called Prism, which was a triangulated three-dimensional tile that initially was going to be a small section. We decided to mould that all in one section, and that gave us the confidence and inspiration for creating a larger, softer, more curtain-like product.
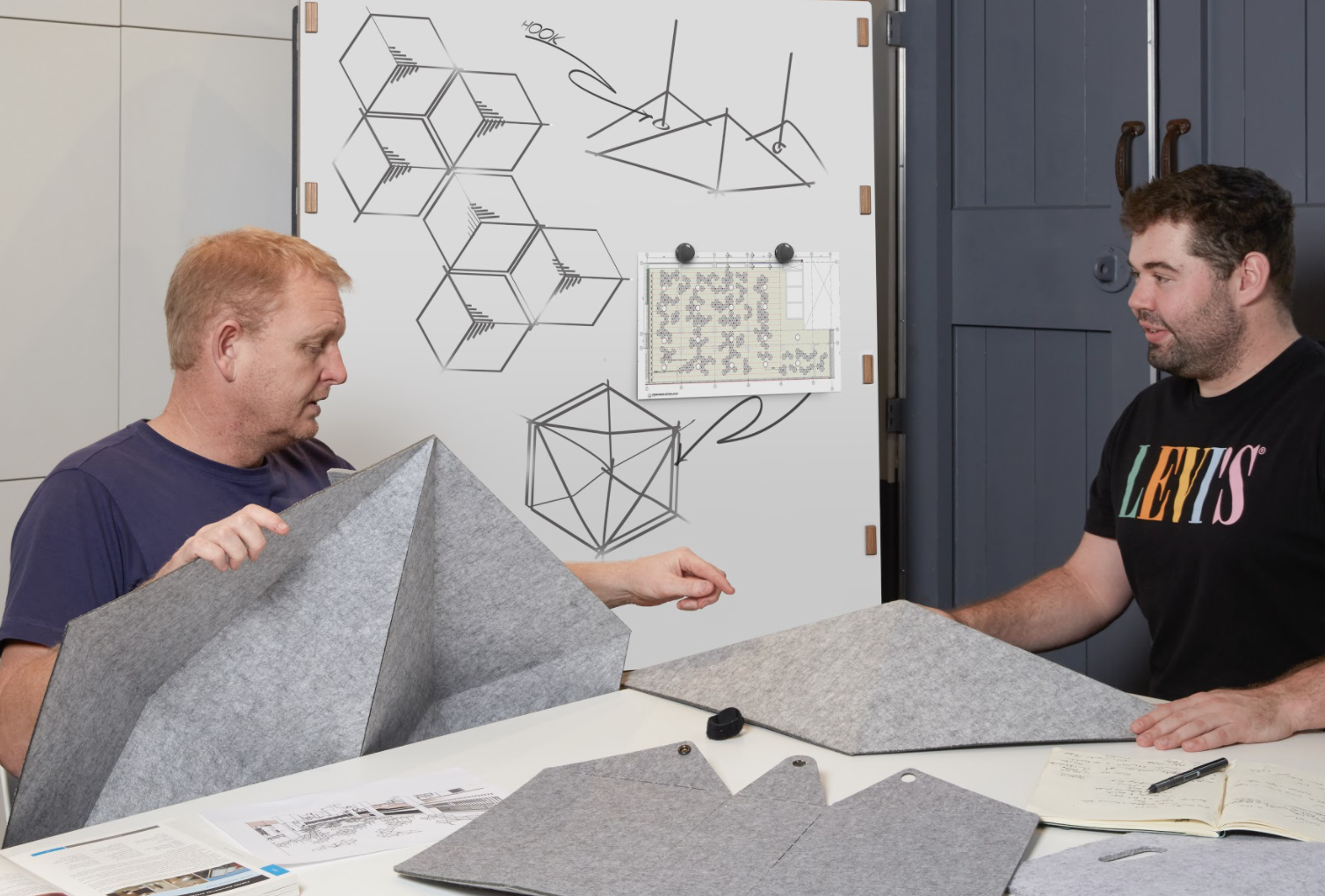
What were the key design challenges?
The scale of Swell, being 2.7 metres high and one metre wide, was one of the biggest and most difficult challenges to overcome. We had to build specialist machinery, and we didn't really know how much contraction or shrinkage we would get from the material because of the processes; you warm the material, and then you press it, and then it cools down, and it stays in that state. And each material, whether it is PET, whether it's felt, whether it's textiles - all react differently to different temperatures. So there's a bit of a black art in terms of being able to perform such large panels like this within the press and machinery.
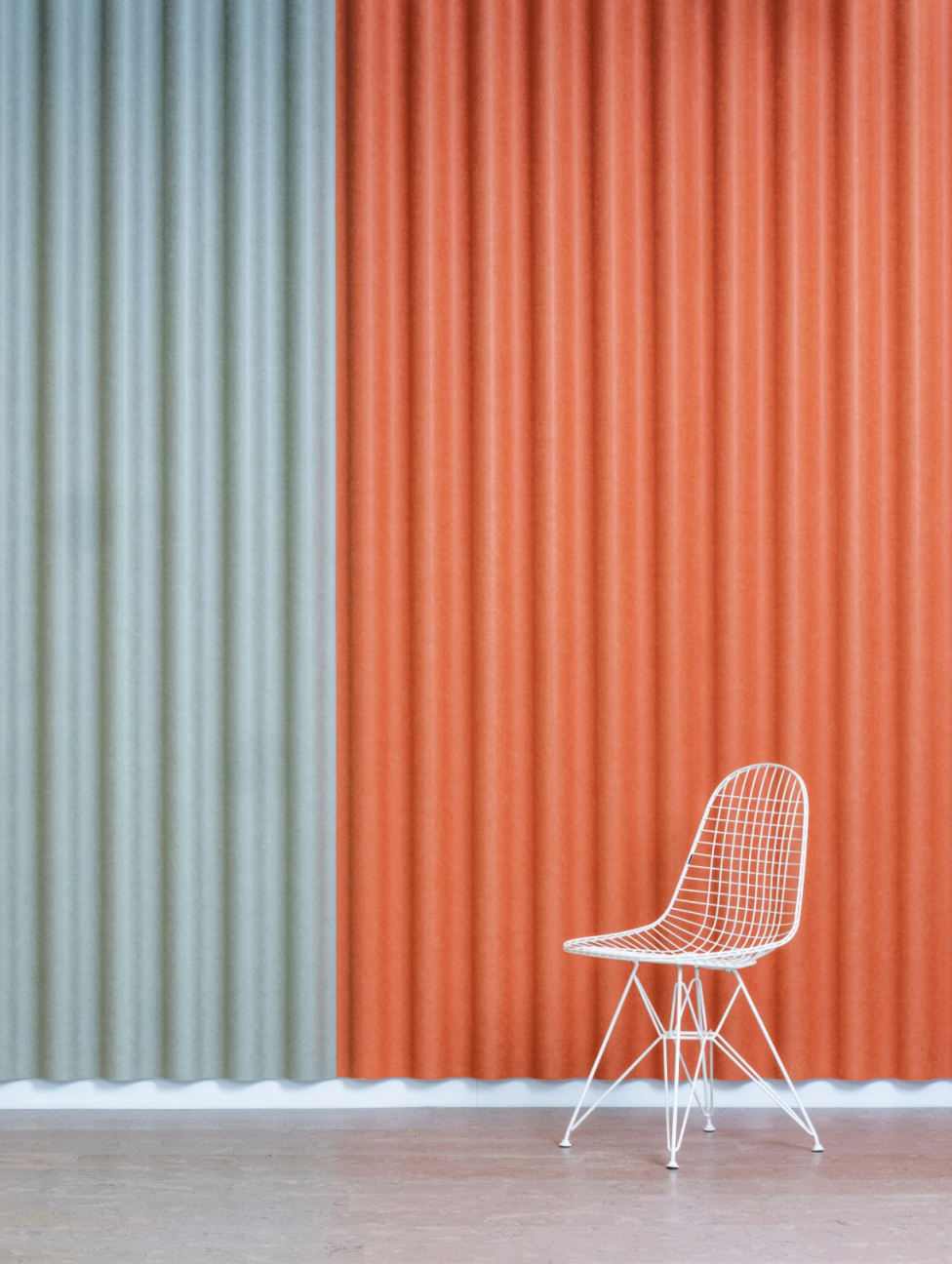
What makes Swell different?
Market intelligence was telling us that people wanted to cover lots of walls with acoustic materials, and they wanted to make a curtain-like consistent shape. So with Swell, the radius on the internal and the external is consistent, so when you put the panels next to each other you can do a run to infinity if you wanted to, with a seamless joint.
How do you see Swell developing further?
At the moment, we've got opportunities to integrate lighting, plus we're looking at ceiling based products and we are experimenting with the factory to see whether we can make some three-dimensional versions of the product. These will hopefully come to fruition sometime this year.
How did you achieve the seamless solution?
The depth and the size of the panel were critical to being able to fit within the machine so that we could cut accurately for the panels to join side-to-side. Because the circles are concentric, the tangency points match whether on the down-point or the up-point. That was one of the key considerations of the depth and radius of the panel.
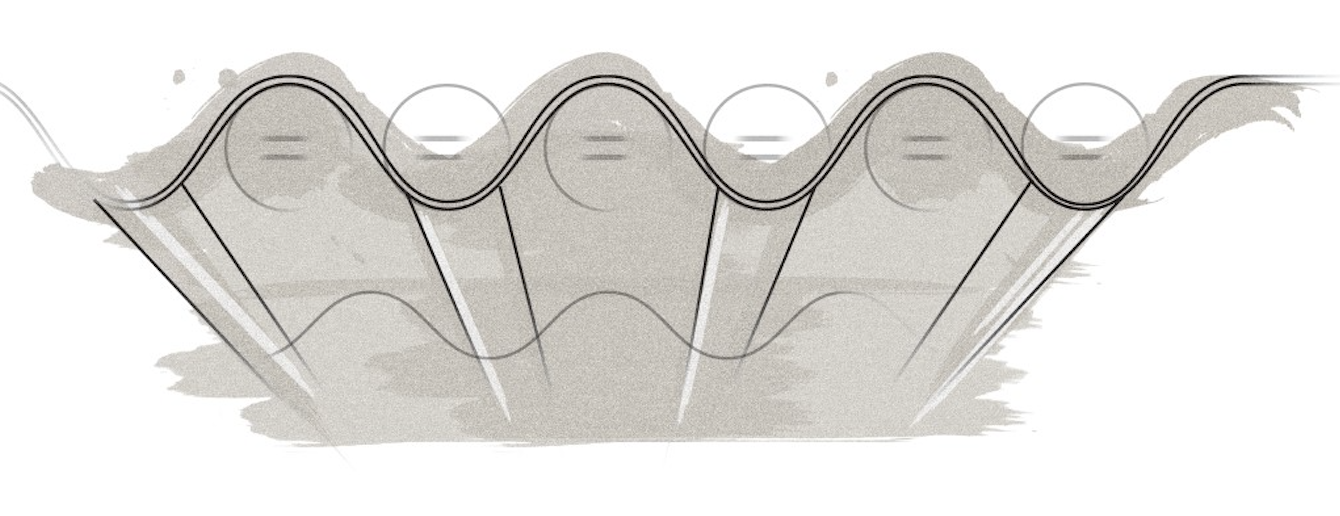
Tell us about the material development.
The material is flat at the beginning of the manufacturing process. We can then laminate different materials on top of the surface before we produce it three-dimensionally. We are experimenting with lots of different materials and substrates to be sat on the front, whether that's fabric, cork, leathers, and that's something that will be an ongoing development for Swell.
How does the framework behind Swell work?
The framework behind Swell is a steel fabricated section. That allows us to create a space - a void, which allows us to get better acoustic performance. It also allows us to control from curvature to flat so that the junction between the tangency to straight panel matches perfectly.
What makes Swell unique ?
The scale of the product was probably the most unique thing about the project. In all the compression moulds that we've created, we've never done anything this size or scale. To produce bespoke machinery and bespoke presses, to get the 2.7 x 1-metre size was probably the highest risk project we've ever done. For the client to then invest knowing that there was a chance that it wouldn't work; well, all credit to The Collective for taking that risk, because it really was out of everybody's control. We didn't really know until the first machine pressed the first panel, whether it worked. Thankfully it did.
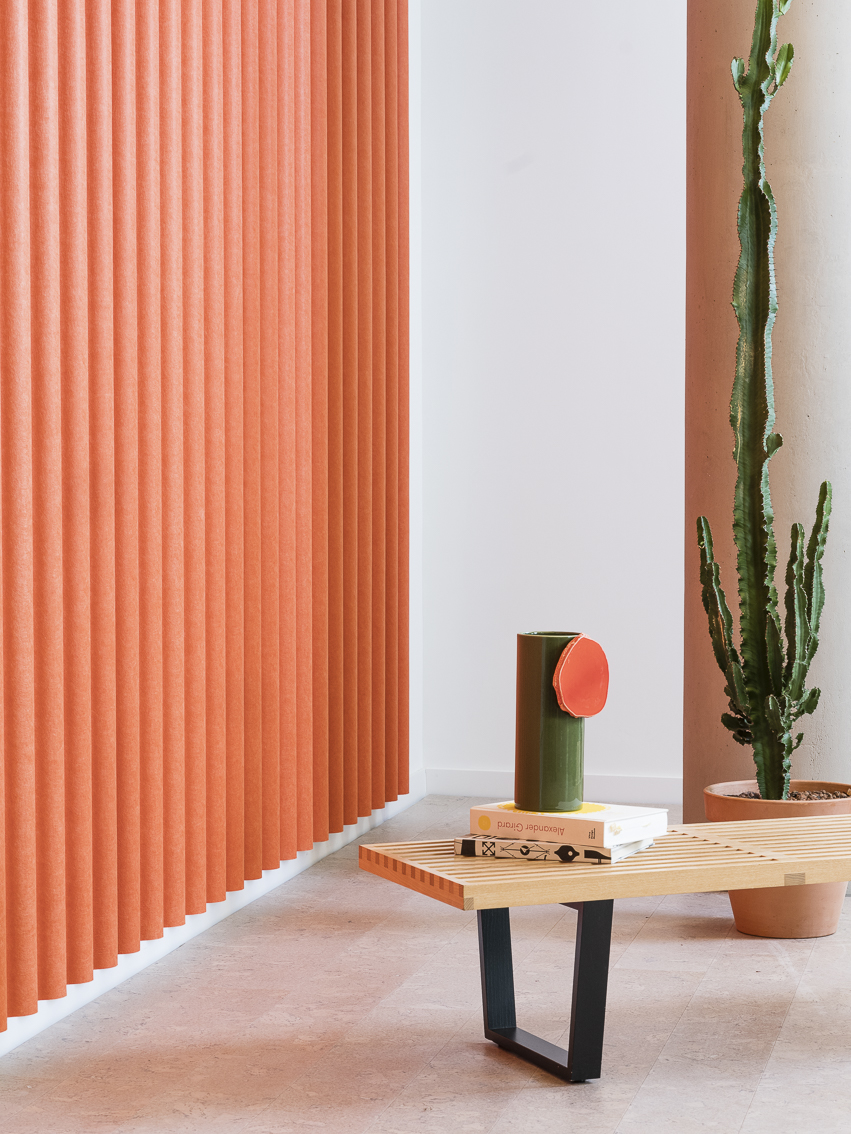
What do you think of the Swell installation behind you?
I think it looks amazing, and it's exactly how we wanted the product to be. Seamless joints, huge scale panels covering metres and metres of walls. I think The Collective has been really brave and it's shown from the response from the marketplace. We've had some big corporate clients already order hundreds and hundreds of these panels, and it's going to be a real commercial success, and I'm really pleased for everybody in the team.

SWELL timelapse installation film
Designer, Jones & Partners, 2021
Photo & film credit : Igor Emmerich, 2021
Furniture courtesy of Vitra